国际能源报告显示,2006年电子电机的能耗为全球电能消耗总量的46%,相当于6040 Mt CO2排放量 。这导致人们要求电机驱动器 制造商新增高级控制功能和工具,以便优化系统能效。在工厂生 产系统中优化能效的新电机驱动器生态系统已得到了全球范围内 的广泛认可。对于欧洲来说,得益于节能政策,工业电能消耗量 呈现出每年1%的下降趋势。
工厂中最常用到电机的地方是电泵、风扇、压缩机和运输机,且电机在这些应用中大多属于标准产品。小型机器设备中使用的 小型电机(低于0.75 kW)占全球存量的90%,但电机能耗不到总量的 10%。然而,中等尺寸(0.75 kW至350 kW)的工业电机几乎占全球电 机能耗的70%。在一个典型应用中,仅有50%的系统能耗转换为 有用的机械能,这引起了全球能源法规制定者和厂商的重视。过 去几年来,美国、中国、欧洲和其他地区的监管机构引入了最低 能耗性能标准(MEPS)。优质电机的额定能效等级现在可从最低功 耗范围时的80%到最高时的96%,因此厂商开始在电机以外寻求 节能手段。
图1描述了现代工厂中自动化机器或过程的主要元素。这种方式 提供了优化机器运行和过程的全新思路,将能效和生产率提升到 新的高度。
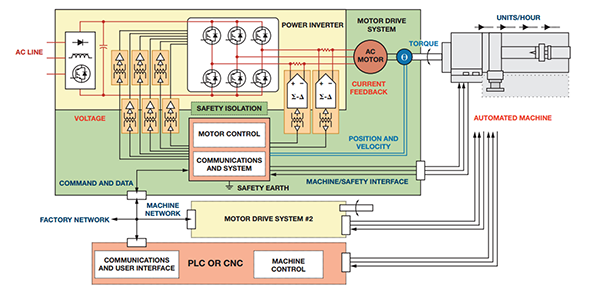
电机的效率和总体生产过程由多个控制层决定。
第一个控制层调 节功率逆变器的开关顺序,控制电机电压和电流以及最大扭矩生 产率。
第二层是位置和速度控制器,高效率运作机器。
在过程设备中,它可以驱动最优泵流速;而在自动化设备中,它可以是执 行装配功能的速度或位置命令序列。如果是后一种情况,则速度 控制的响应时间相比扭矩生产率而言对机器控制器更为重要。通 信和系统层的重要性日益凸显,因为多个电机现在通过高速数据 网络同步,并连接工厂网络。过程管理器可在需要的时候顺序开 启机器,而不是让它们在空闲模式下等待。联网安全功能实现 设备的高效启动和停止,最大程度缩短停机时间。工厂管理人 员跟踪电机驱动器的操作,并诊断数据,以便改善过程能效和 可靠性。
高效扭矩产生: 算法和以太网
电机效率是任意给定速度和终端电压下每安培所产生扭矩的函数。电子电机通过试图将其内部磁场拉至对齐位置的力产生扭 矩。在图2交流电机中,这些力通过定子和转子磁场的相互作用 产生。当定子电流与转子运动同步时,交流电机产生恒定的扭 矩,维持连续场的不对齐状态。交流电机速度与电机电流频率直 接相关,且需要使用可变频率电压源才能进行速度控制。当转 子和定子的磁场对齐误差达到最大时,效率最高。电机效率还取决于电机结构,尤其是转子磁场结构。在异步感应电机中(AIM), 电流流过转子和定子绕组,部分最小定子电流消耗在使磁芯磁化 上。永磁同步电机(PMSM)效率更高,因为它们无需任何电流来使 转子磁场磁化。借助于突出的磁芯结构,超高效率内部永磁(IPM) 电机能够产生额外的扭矩。
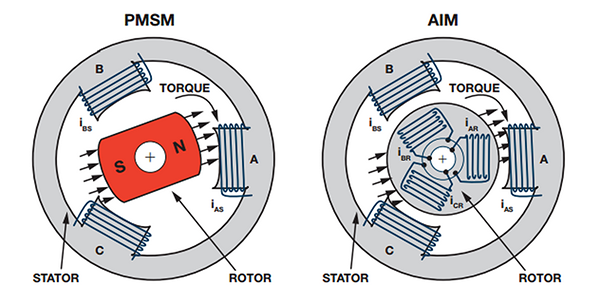
以上所有电机都用于工业中,具体取决于功率和应用要求,但由于结构简单、使用方便,异步感应电机是目前为止最常用的电机。永磁同步电机具有较高的扭矩重量比,其低惯性转子结 构使其非常适合自动设备的高动态控制应用。然而,AIM可在直 接连接三相交流线的时候启动,并且可以使用简单频率逆变器 控制速度。以前不像现在那么重视效率,一般是直接把风扇、 泵或压缩机连接到交流线上,并通过阻尼器、阀门或简单的开/ 关控制这个过程。以50%速度运行时,开环频率控制可将离心 泵的功耗降低至不足全功率的20%;而使用开/关控制使流速下 降到50%时,功耗为全功率的50%。这种系统效率提升促使厂商 改造现有固定速度电机应用的变频器。近来,高级算法可以通 过微调定子电压来调节转子磁场,进而优化效率。驱动器制造 商现已开始提供标准驱动箱,可配置为各种电机型号与类型。
最新的模拟和数字信号处理设备甚至在成本敏感型变频器应用中 引入了高级控制功能。估算算法仅测量定子电流和电压便可计算 出转子磁场的角位置。这些无传感器控制算法简化了高效率IPM 电机的部署,并最大程度提升压缩机和运输机等应用的处理效 率。诸如绕组机器或大型泵等较高功耗应用依然倾向于采用感应 电机,但500 kW电机的典型效率可高达96%。这些驱动器内置的算法通常可以优化电机效率,并监控驱动器的工作情况。一般而 言,这些驱动器采用串行现场总线连接,允许本地PLC记录运行 和诊断数据。一个不断增长的趋势是使用诸如Ethernet/IP或Modbus TCP等工业以太网协议将驱动器连接到工厂网络中,以便通过协 调多个驱动器运行而改善效率。
高效运动控制: 精确隔离和通信
精确运动控制加上精确通信时序,可缩短机器生产周期,降低生产每个部件所消耗的能源。由于设备的资本投入,这一点在机器 生产率和质量通常比电机能效更重要的自动化系统中很重要。驱 动器制造商通过PMSM伺服电机和驱动器支持自动化应用;这些 电机和驱动器设计为可在速度和位置控制中实现快速响应和高精 度。
快速控制处理器配合精确电压驱动器和电流反馈,可提供 平滑的动态扭矩控制。功率变频器中的高电压和电流对电路设计 人员来说是一种挑战,因为隔离电路必须满足严格的电气安全标 准。高速磁隔离技术支持模拟和数字信号电压的安全隔离,且不 会降低速度或精度性能。编码器处内置的精密模数转换器可提供 高达24位分辨率的位置反馈,从而在低至1 RPM的速度下实现高动 态速度控制。这种性能水平可支持的自动化应用有:精密机器部 件的多轴铣磨、精细几何集成电路的装配,或手机部件的注塑成 型。除了控制精度,电机运动时序还需紧密同步,因为时序误差 直接导致多轴位置控制的轨迹误差。诸如PROFINET和EtherCat等同 步工业以太网协议采用经过修改的以太网网络接口,支持数据的 实时同步,且时钟抖动低至1 μs。这些网络接口支持全部两种同步 运动控制,可实现生产系统管理的高生产率和工厂网络连接性。
工程效率:快速定制
建模工具可让驱动器公司为最终应用快速定制控制算法,无需在工厂中投入大量试生产和误差调谐。
自动化机器是复杂的互连系统,需要跨学科工程团队的支持。图 3仅显示支持开发自动化设备开发所需的部分关键设计功能。一 般而言,很多这类工程师供职于不同的公司,因此供应链上的不 同供应商必须为设计人员的整合工作提供支持。MathWorks等公司提供的建模工具支持完整的系统模型,包括状态控制、运动算 法、电机和机器负载。特殊的电磁和机械设计工具可以生成交流 电机和机器的行为模型,增加系统模型的精度。虽然无法完全自 动化整个设计过程,但可以大幅减少原型制作次数。新电机或机 器的控制算法可在进行原型制作前于仿真平台上完成开发和测 试。自动代码生成工具允许在测试平台上快速部署控制算法。每 一次设计迭代都提供新的数据,改进系统模型的精度。自动生成 的控制代码加上经过验证的系统应用代码,可以用于生产驱动器 系统中。因此,驱动器公司可快速部署针对特定应用优化的新控 制功能,进而优化能效和自动化生产率。
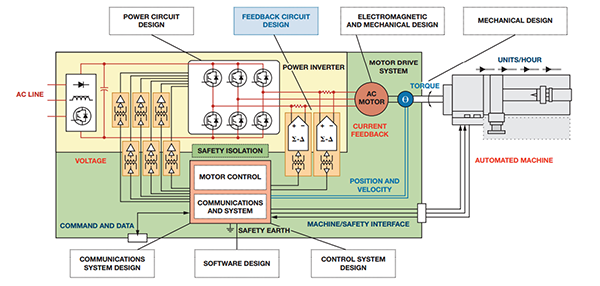
结论
越来越多的工业和仪表应用要求使用精密转换器来实现各种工艺 的精确控制与测量。此外,这些最终应用还要求更高的灵活性、 可靠性和功能集,同时降低成本和电路板面积。元件制造商正在 解决这些难题,并推出了一系列产品来满足系统设计人员对当前 与未来设计的要求。如本文所述,有多种途径可选择合适的元件用于精密应用,每一种都各有优缺点。随着系统精度的提高,人们需要更加注重合适元件的选择,以满足应用要求。