1. 引言
汽车行业的小电机中,小模数蜗杆斜齿轮常用于电动机中的空间运动与扭矩传递,设计人员以电动机设计的目标(高效、低成本、小体积)为设计准则,定出齿轮设计中的各项参数,如传动比、中心距、斜齿轮与蜗杆的最小齿厚,蜗杆齿根圆直径等等。以保证其设计出来的蜗杆与斜齿轮足以承载整个电机运行周期内的力矩、转速、使用寿命等要求。可以说电机中的齿轮设计,是一种服务型设计,其参数设计主要服务于使用的电动机。
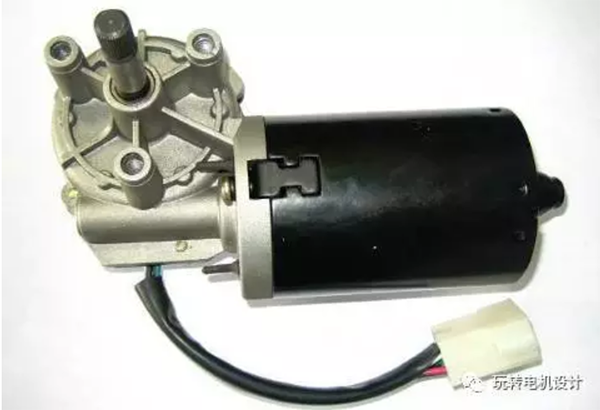
2. 基本参数的设计方法
以实际设计为例,我们将设计的电机体积目标为基准,便能定出减速器壳体的内型腔体积大小,由此可以大致确定蜗杆斜齿轮的中心距。我们以针对的电机性能为基准,再根据需要输出的最终转速与力矩,确定齿轮设计中的传动比。
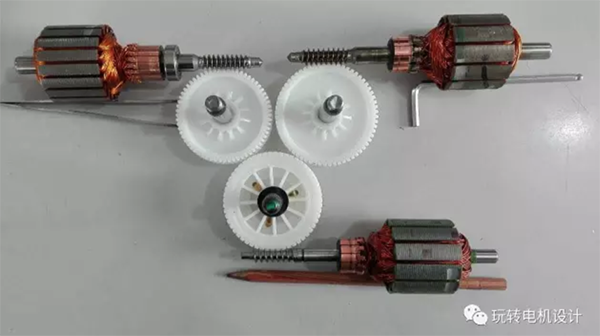
2.1 蜗杆斜齿轮模数的确定
以单头蜗杆为例,得到传动比就能得到斜齿轮的齿数。在得到中心距与齿数的情况下,我们便能根据“结构定模数”的设计思路,设计出适合该电机的斜齿轮模数,即:
M = 2a / (Z1+Z2)
一般来说,非标模数斜齿轮中m可以取M±0.1内的任何数字,m的取值直接关乎齿轮的端面重合度大小,在其它参数不变时,m取值越小,总重合度εy:
εy= εα + εβ …… ①
其中:εα=0.5π [z1(tanat1 – tana’t)± z2(tanat2 – tana’t)] …… ②
εβ=btanβ /πmt =bsinβ /πmn …… ③
越大,根据国外学者Niemann与 Unter-berger发表的关于直齿圆柱齿轮重合度与噪声的实验研究结果表明重合度对齿轮的啮合噪音具有重要的影响,该实验表明:端面重合度增大到2时,噪声级将急剧减小;当端面重合度超过2至2.2时,噪声级将重新增加。在斜齿轮中,端面重合度对噪音的影响要略小于直齿轮,所以定模数往往需要与实际经验相结合,如考虑我们的电机需要承受大力矩,则可选择将重合度略微提高,如果优先考虑噪音,则将重合度控制在2-2.2即可。
2.2 蜗杆斜齿轮压力角与螺旋升角的确定
齿轮压力角影响齿轮的齿截面形态,因此我们常把压力角称为齿形角(α),压力角决定了齿轮的齿根齿顶厚度,压力角越大,齿根越肥,齿顶越薄,反之压力角越小,齿根越瘦,齿顶越厚,在金属圆柱直齿轮传动中,一般我们使用20°压力角。而在小模数蜗杆传动中,齿厚较薄,我们需要将压力角适当减小,中小电机中通常取10°-15°之间的压力角。 另外,斜齿轮啮合的充要条件是参与啮合的两个齿轮法向基圆齿距相等, 即:
π m1 cosα1 = π m2 cosα2
所以当蜗杆和斜齿轮的模数相等时,压力角也必须相等。实际生产中,需要根据能够接受的齿顶厚度(不宜过尖)和齿根厚度(不宜过薄)以及以往的设计经验来确定我们的压力角。

螺旋角,又叫螺旋升角(γ或β),它直接参与斜齿轮的参数运算,因为有螺旋线的存在,斜齿轮被分为了法向参数与轴向参数两种计算模式,其中就利用cosγ来互相换算。单头蜗杆螺旋角一般很小,齿距较小。随着减速比的减少,蜗杆头数增多时,螺旋角增大。我们在使用软件设计参数时,当齿数传动比、中心距、模数确定时,螺旋角也就确定了。同样条件下,模数越小时,螺旋角也会跟着减小,齿的分布越密集,齿轮的重合度越高,减速比增加。螺旋升角一般设计在几度到十多度不等,大螺旋角一般出现在多头蜗杆传动中,有利于增加电机传递效率。单头蜗杆斜齿轮传动效率比较低,一般在50%-60%左右。
螺旋角与压力角在齿轮啮合的滑动率与传递效率上有着非常重大的影响,目前还没有学者能完全正确的诠释两种角度与传递效率的详细关系。法国学者 昂里奥在《齿轮的理论与实践》(王兆义 译)一书中用实验法阐述了斜齿轮传递效率与螺旋升角的关系,他指出,当螺旋角小于45°时,传递效率随着螺旋角的增大而增大,当螺旋角大于45°时,传递效率随螺旋角的增大而减小。但实际使用中,我们不可能使用如此大的螺旋角来设计参数,一般设计为5°-15°。因此实际使用中的传递效率往往不可预计或控制,只能尽量设计适合自己电机使用的螺旋升角。可见蜗杆斜齿轮的参数没有绝对的优劣之分,而只有最合适当下产品的参数这个说法,这也是使得蜗杆斜齿轮日趋成为“服务型设计”的原因之一。
这里还需要提一点就是蜗杆在承受大力矩实验时,压力角与螺旋角的大小也会影响其受力的方向,若螺旋角与压力角很大,那么蜗杆受偏移力影响较大,如果此时蜗杆的齿根强度较弱,或者减速器壳体刚性不足,则会发生蜗杆斜齿轮中心距增大,齿与齿的分离,造成剃齿。如果螺旋角与压力角比较小,此时蜗杆受轴向力较大,在采用轴承与蜗杆过盈配合的工艺装配中,就需要对轴承的脱出力有较高的要求,方能保证蜗杆在大力矩实验中不会前后窜动。
2.3 齿顶齿根高的设计
当减速器壳体把中心距大小确定时,蜗杆与斜齿轮的齿顶、齿根高数值也就开始在一定的范围内逐渐成型,蜗杆的齿顶与斜齿轮的齿根以及两者的顶隙,或者说蜗杆的齿根与斜齿轮的齿顶以及两者的顶隙,就构成了我们所要的中心距,也就是说,中心距一定时,我们在确定了顶隙的情况下(一般为0.2~0.4个模数)剩下的就是分配双方的齿根齿顶高。此参数的设计需要与自己公司的工艺紧密结合。
这里举个例子:电机设计成型时,已经敲定蜗杆用哪一种尺寸的轴,如当蜗杆决定采用Ф8的轴时,若采用旋风铣加工,那么蜗杆齿顶高宜定为7.93-7.98左右,齿顶高定的太低,加工时需要先将轴削小,再加工齿形,这样不光浪费了材料,还大大浪费了加工时间。但也不宜刚好定为Ф8,因为难以保证光轴上面没有瑕疵,所以还是需要往下走一点,略微处理一下表面,以保证设计的蜗杆在加工后齿顶光滑无损坏。在定好齿顶参数后,根据所需要的重合度定出齿高即可。
2.4 等强度设计(齿厚分配与变位系数)
在前三项的参数设计完成后,蜗杆斜齿轮的大致齿形已经确定,此时我们需要考虑是否需要变位与变更齿厚。很多小型直流电机,通常使用金属蜗杆配塑料(或为聚甲醛或为尼龙)材质的斜齿轮,那么很显然金属件与塑料件强度是不一样的。因此我们需要适时的将塑料斜齿轮的齿厚增肥,将金属蜗杆的齿厚减薄,以达到一种双方强度大致相等的平衡。这里介绍一种简单的变位方法:即锁定双方齿根齿顶以及顶隙参数,仅仅通过调整径向的变位系数来调整双方齿厚,将塑料齿轮增肥,金属齿轮减薄,一般只需要将分度圆处的塑料齿厚与金属齿厚分配比为6:4或7:3则可达到一种等强度的平衡。
2.5 公差与侧隙的选取
公差的选取决定了我们蜗杆斜齿轮啮合时侧隙的大小,我们在前面设计参数时,无论是基本参数还是齿厚分配,都以0侧隙为基础去考虑,而实际使用上,我们必须要考虑侧隙的影响,目前也没有太多的理论可以指导设计齿轮时需要多大的侧隙,一般我们考虑到齿轮制造的误差,特别是注塑斜齿轮收缩不均时,公差带会比较大,同时考虑中心距的装配误差,为避免出现负侧隙的情况,我们需要在设计齿轮齿厚时,标注为负公差,留出一定大小的侧隙。在要求正反转的电机中,齿轮侧隙不能留得太高,最大不宜超过0.1mm,防止换向时出现撞击声。单向转动的齿轮中,设计侧隙需控制在为0.03-0.12mm。
蜗杆的齿厚公差、注塑斜齿轮制造的齿厚公差、中心距装配工差,决定了侧隙的公差带大小。制造与装配精度越高,侧隙的一致性就越好。
2.6 齿轮的修形
一般而言的齿轮修形,是指渐开线齿形修整,理论上无论是渐开线圆柱直齿轮还是蜗杆斜齿轮,双方齿形都是渐开线,但是在金属蜗杆配塑料斜齿轮中,模数很小,并且为了方便加工,降低成本,大多使用阿基米德蜗杆近似代替了渐开线蜗杆。这样原本两个鼓凸的齿形啮合就变成了一个平齿与一个凸齿啮合。塑料齿轮在受力变形时,与蜗杆的啮合斑点会增大;如果两个都是鼓凸齿形,则啮合斑点大小受力变化较小,而当蜗杆的法向截面变成平齿时,啮合斑点大小受力变化就会增大。为了消除这个不良影响,又为了保证蜗杆加工的低成本,设计人员往往选择将斜齿轮原本的渐开线做的更加鼓出来,这样是为了反向弥补阿基米德蜗杆相对于渐开线蜗杆的误差。
齿轮修形不属于齿轮的参数设计,而且后期的参数检测结果也会跟标准的渐开线齿形有一些差距。这需要设计人员具备有比较丰富的齿轮设计经验。
3 算例
现需一款带减速机构小型电机,要求14V电压下,减速机构终端工作负载为3nm,负载下转速为55转/分,设计限制:减速器壳体最大外径不超过70mm。1. 根据工作负载输出功率选择或重新设计一款匹配的电机,若为永磁直流电机,则可选择负载下额定输出功率约为P=(3*55)/(9.55*0.45)的电机。
2. 由减速器壳体尺寸限制确定斜齿轮最大外径,考虑到设计裕度与壳体厚度,本案例取62-63mm。
3. 估算电机输出端堵转的最大力矩,根据堵转力矩大小选择蜗杆(电枢轴)直径,本案例取Φ10。
4. (62.5+10)/2=36.5mm 取中心距为35mm。
5. 为增大传动效率,可设计为双头蜗杆,则Z1=2 ,若选定的电机负载下转速为2800转,则传动比为2800/55=50.909,则斜齿轮齿数Z2=50.909*2=101.82 取Z2=102,传动比51。
则蜗杆斜齿轮基本尺寸如下:
蜗杆直径:Φ10
斜齿轮外径:62.4
蜗杆头数Z1:2
斜齿轮齿数Z2 : 102
传动比:51
中心距a:35mm
根据结构定模数:M=2a/(Z1+Z2)=0.67mm
为增加重合度可取模数M=0.6, 为降低重合度可取模数M=0.7
本例中取:M=0.6mm
为保证蜗杆齿的法向齿顶保有安全厚度,压力角(10°-15°)不宜过大,本例取压力角 :α=12°
双头蜗杆传动,本案例螺旋升角取:β=9°
全齿高度可取2.8-3mm,顶隙系数C=0.35
则蜗杆齿根直径为7.18mm,斜齿轮齿根直径为59.58mm
基本参数设计完毕。
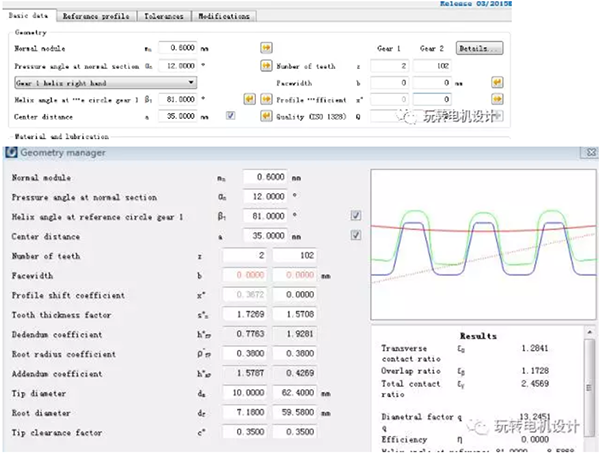
根据等强度齿厚分配原则调整径向变位系数,本例中通过调整变位系数将蜗杆分度圆齿厚分配为0.69mm,塑料斜齿轮分度圆齿厚分配为1.288mm。
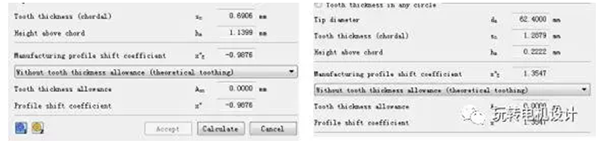
齿轮公差:蜗杆为机加件,法向齿厚公差可控制在0.03以内,注塑斜齿轮为模具件,考虑其存在的收缩率,可将其齿厚公差放松至0.05以内,双方的齿厚负公差以及中心距装配公差取值决定了齿轮啮合的侧隙值。
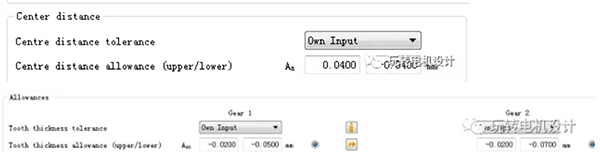
本例中蜗杆齿厚公差为 ﹣0.02~ ﹣0.05 斜齿轮齿厚公差为 ﹣0.02~﹣0.07
中心距装配误差由该公司自己的工艺水平决定。齿根齿顶公差给0~﹣0.1即可。
设计完参数后生成的齿轮齿廓:

3D模型:
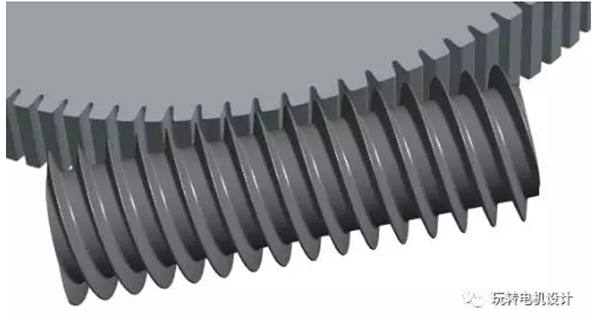
齿轮动态啮合斑点:
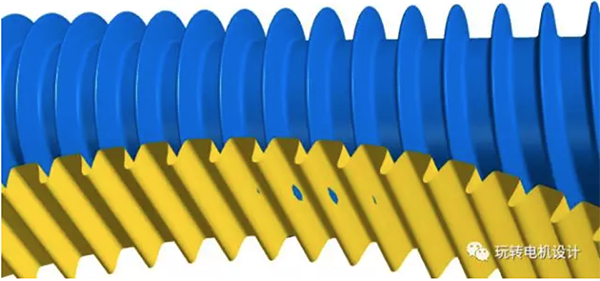
最后,抄书给供应商加工时需要用到的一些其他基本参数:
1,法向齿顶厚,导程。
2,蜗杆:需提供棒量直径与三针跨测量距,斜齿轮:需提供跨齿数与公法线测量长度。
3,渐开线起始圆直径,蜗杆退刀纹区域长度。
4,蜗杆的有效啮合长度,斜齿轮的有效啮合厚度。
5,蜗杆斜齿轮各项跳动公差数值