Wenshuai Liao 和 Luis Orozco
节能和环保在我们的日常生活中扮演着重要的角色;而随着价格亲民的混合动力汽车和电动汽车的发布,人们的这些意识进一步得到了提高。这两项技术均使用大量充电电池,其中高品质、高功率的锂离子电池单元代表了目前为止最佳的解决方案。这些电池广泛用于笔记本电脑、手机、数码相机、摄像机和其他便携式设备中,但生产效率并未成为一个主要问题,因为这些电池的容量较低,通常为每单元或每组低于5 安时(Ah)。一个典型的电池组由不到一打的电池单元组成,因此匹配也不是什么重要问题。
实现节能的一种方法是在非高峰时段储存电能,补充高峰时候的 用电需求。用于车辆或电能存储的电池具有高得多的容量,通常 为几百Ah。这是通过大量小型电池单元或一些高容量电池来实现 的。例如,某种型号的电动汽车采用大约6800 个18650 锂离子电 池单元,重达450 kg。由于这个原因,电池生产需要制造速度更 快、效率更高以及控制更精确以满足市场的价格需求。
锂离子电池制造概述
图1 显示锂离子电池制造过程。下线调理步骤中的电池化成和测试不仅对电池寿命和品质产生极大影响,还是电池生产工艺瓶颈。
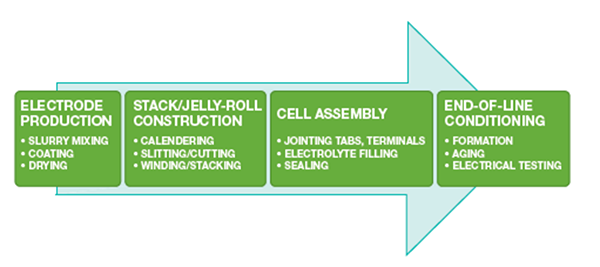
就目前的技术来说,必须在电池单元级完成化成,这可能需耗时数小时甚至数天,具体取决于电池化学特性。在化成时通常采用0.1 C(C 是电池容量)电流,因此一次完整的充放电循环将需要 20 小时。化成可占到电池总成本的20%至30%。
电气测试通常使用1 C 充电电流和0.5 C 放电电流,这样每次循环依然需要一小时的电池充电时间和两小时放电时间,且一个典型的测试序列包括多个充放电周期。
化成和电气测试具有严格的精度规格,电流和电压控制在±0.05%以内。作为比较,为便携式设备(比如手机和笔记本电脑)的电池充电时,精度可能仅为±0.5%(电压)和±10%(电流)。图2 显示典型的锂离子充放电曲线。
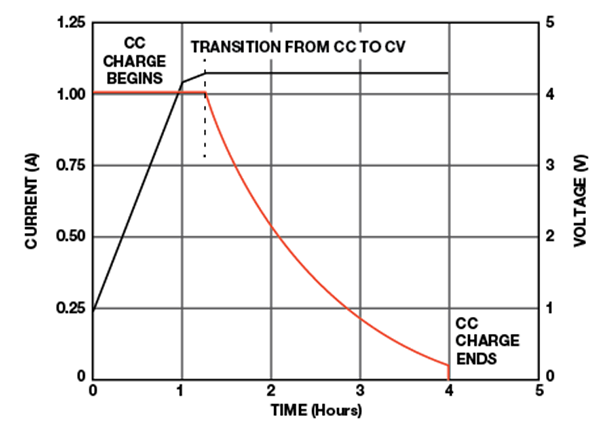
线性或开关化成及测试系统
选择制造方法时,需考虑到的最重要因素是功效、系统精度和成本。当然,其他因素——比如小尺寸和易于维护——也十分重要。
为满足电池制造中的高精度要求,系统设计人员原来会采用线性电压调节器;这样做可以轻松满足精度要求,但效率较低。用在低容量电池生产可能是一个较好的选择,但某些制造商依然可以 采用开关技术来凸显他们的优势。最终决策将是效率、通道成本和电流之间的取舍。原则上讲,开关技术能够以相同的单通道成本为容量超过3 Ah 电池单元提供更高的效率。表1 显示各类电池单元的功率容量和最终用途。
表1. 线性和开关系统对比

为了以更低的成本更快地生产电池,系统在化成和测试阶段使用 了成百上千的通道,其测试仪拓扑取决于系统的总能源容量。测试仪中的大电流会导致温度大幅上升,增加随时间推移而维持高测量精度和可重复性的难度。
在放电阶段,保存的电能必须要有地方能够输出。一个解决方法是把电池放电到阻性负载,将电能转化为热能而浪费。一个更好的解决方案是循环使用这些电能,通过精密控制电路将电流从放 电电池单元馈入另一组充电电池单元中。这项技术可以显著提高测试仪效率。
一般而言,通过每个电池单元的直流总线和双向PWM 转换器,可实现电能平衡。直流总线电压与特定系统有关,电压值可以是12 V、24 V 甚至高达350 V。对于同样的电量而言,由于存在导 通电阻,较低的电压总线具有较高的电流和较高的损耗。较高的电压会产生安全性方面的额外担忧,并且需要使用成本高昂的电源和隔离电子器件。
图3 显示可实现电能循环的典型开关拓扑。各电池单元之间(红色路径)或各电池单元之间的直流链路总线(绿色路径)可实现电能的循环利用,也可将其返回电网(紫色路径)。这些灵活的 高效率设计可降低生产成本,并获得90%以上的效率。

虽然这项技术具有很多好处,但也存在一些技术难题。电压和电流控制环路速度必须足够高,并且必须能随时间和温度的变化保持高精度。使用空气冷却或水冷却会有所帮助,但采用低漂移电 路更为重要。该系统包括开关电源,因此必须以合理的成本抑制电源纹波。另外最大程度缩短系统校准时间也很重要,因为系统关断进行校准时不会产生收益。
控制环路设计:模拟或数字
每个系统都提供一个电压控制环路,还有一个电流控制环路,如图4 所示。对于汽车中使用的电池单元,汽车加速时需要快速斜升电流,因此测试时必须对其进行仿真。快速变化速率和宽动态范围让电流控制环路的设计变得十分棘手。
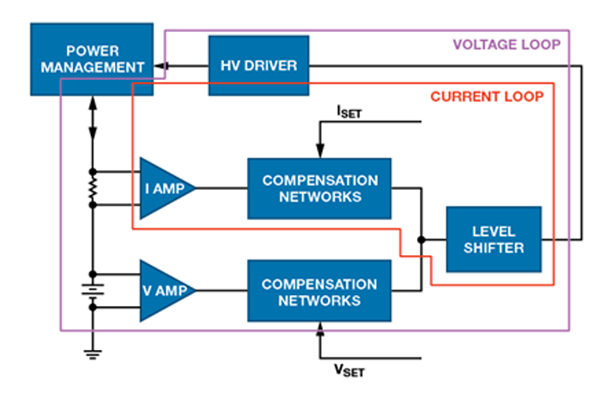
一个系统需要四个不同的控制环路,这些环路可在模拟域或数字域中实现:恒流(CC)充电、CC 放电、恒压(CV)充电和CV 放电。需干净地切换CC 和CV 模式,无毛刺或尖峰。
图5 显示数字控制环路的框图。微控制器或DSP 连续采样电压和电流;数字算法决定PWM 功率级的占空比。这种灵活的方式允许进行现场升级和错误修复,但有一些缺点。ADC 采样速率必须 超过环路带宽的两倍,大部分系统采样速率为环路带宽的10 倍。这意味着,双极性输入ADC 必须工作在100 kSPS,才能采用单个转换器和分流电阻涵盖充电和放电模式。某些设计人员在速度和精度更高的系统中采用16 位、250 kSPS ADC。作为控制环路的一部分,ADC 精度决定了系统的整体精度,因此选择高速、低 延迟、低失真的ADC 很重要,比如6 通道、16 、250 kSPSAD7656.

在多通道系统中,每个通道一般要求使用一个微控制器和一组专用ADC。微控制器处理数据采集、数字控制环路、PWM 生成、控制和通信功能,因此它必须具有非常高的处理能力。此外,由 于处理器必须处理多个并行任务,PWM 信号中的抖动可能会引起问题,尤其是PWM 占空比较低时。作为控制环路的一部分,微处理器会影响环路带宽。
图6 中的电池测试系统采用模拟控制环路。两个DAC 通道控制CC 和CV 设定点。AD8450/AD8451 用于电池测试与化成系统的精密模拟前端和控制器可测量电池电压和电流,并与设定点进行比较。CC 和CV 环路决定MOSFET 功率级的占空比模式从充 电变为放电后,测量电池电流的仪表放大器的极性转,以保证 其输出为正,同时在CC 和CV 放大器内部切换可选择正确的补偿网络。整个功能通过单引脚利用标准数字逻辑控制。
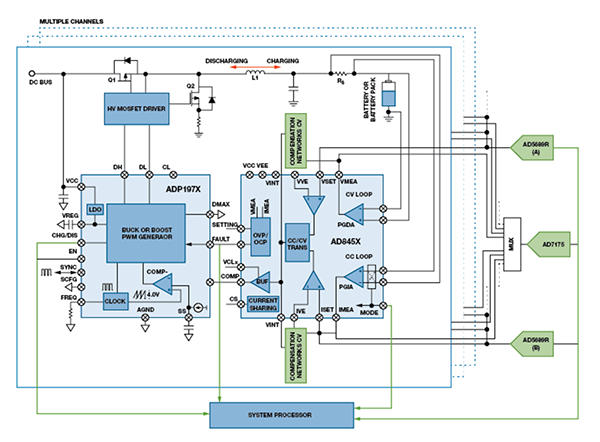
在此方案中,ADC 监测系统,但它不属于控制环路的一部分。扫描速率与控制环路性能无关,因此在多通道系统中,单个ADC 可测量大量通道上的电流和电压。对于DAC 而言同样如此,因此针对多个通道可采用低成本DAC。此外,单个处理器只需控制CV和CC 设定点、工作模式和管理功能,因此它能与多通道实现接口。处理器不决定控制环路性能,因此并不要求高性能。
ADP1972 PWM 发生器使用单引脚控制降压或升压工作模式。模 拟控制器和PWM 发生器之间的接口由不受抖动影响的低阻抗模拟信号构成;而抖动会使数字环路产生问题。表2 显示模拟环路相比数字环路如何提供更高的性能和更低的成本。
表2. 模拟和数字控制环路比较
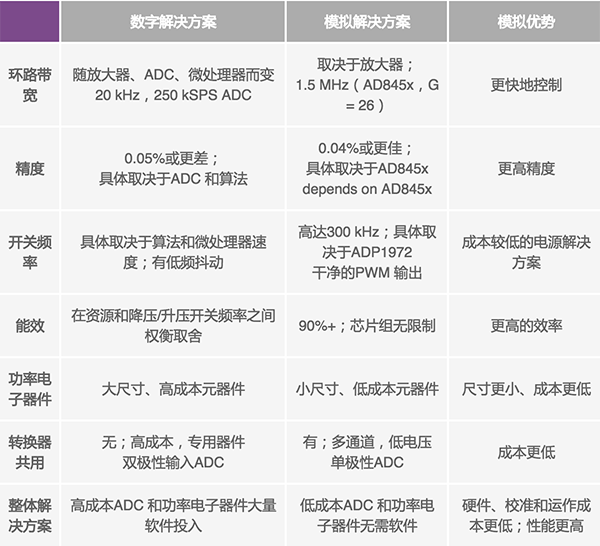
特定温度范围内的系统精度
校准可除去大部分初始系统误差。余下的误差包括:放大器CMRR、DAC(用于控制电流和电压设定点)非线性和温度漂移造成的误差。制造商指定的温度范围各有不同,但最常见的是25°C ±10°C,本文即以此为例。
本设计中使用的电池,完全放电后电压为2.7 V,完全充电后电压为4.2 V;使用5 mΩ分流电阻的满量程电流为12 A;用于。AD8450的电流检测放大器的增益为66;用来测量电池电压差动放大器 增益为0.8。
总系统误差中,电流检测电阻漂移占了相当一部分。Vishay 大金属电阻;器件型号:Y14880R00500B9R,最大温度系数为15ppm/°C,可减少漂移。AD5689 双通道、16 位nanoDAC+™模 转换器,最大INL 额定值为2 LSB,可降低非线性度。ADR45404.096 V 基准电压源,最大温度系数额定值为4 ppm/°C,是在电流和电压设定点之间进行取舍后的理想选择。经电流检测放大器以66 倍衰减后,DAC INL 会使满量程误差增加约32 ppm,基准电 压源引入的增益误差为40 ppm。
电流检测放大器在增益为66 时的CMRR 最小值为116 dB。如果系统针对2.7 V 电池进行校准,则4.2 V 电池将产生40 ppm 满量程误差。此外,CMRR 变化为0.01 μV/V/°C,或者0.1μV/V(10°C 温度范围)。电流检测放大器的失调电压漂移最大值为0.6 μV/°C,因而10°C 温度偏移将产生6 μV 失调,或者100 ppm 满量程误差。
最后,电流检测放大器的增益漂移最大值为3 ppm/°C,而总漂移为30 ppm(10°C 范围内)。检测电阻漂移为15ppm/°C,因此总共增加150 ppm 增益漂移(10°C 范围内)。表3 总结了这些误差 源,它们产生的总满量程误差不足0.04%。该误差很大一部分来源于分流电阻,因此必要时可以采用漂移值较低的分流电阻,以改善系统精度。
表3. 10ºC 范围内的电流测量误差
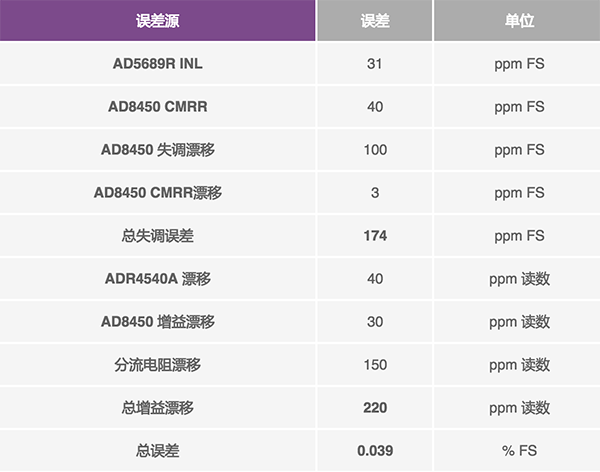
类似地,对于电压输入而言,2 LSB DAC INL 相当于折合到5.12 V满量程输入的31 ppm 误差。若电池电压在2.7 V 和4.2 V 范围内变化,那么差动放大器的78.1 dB CMRR 将产生187 μV 失调误差,或者36.5 ppm 满量程误差。来自CMRR 漂移的额外误差远低于1ppm,可以忽略。
差动放大器的失调漂移为5 μV/°C,或者10 ppm 满量程误差(10°C范围内)。差动放大器的增益漂移为3 ppm/°C,或者30 ppm(10°C 范围内)。基准电压漂移为40 ppm(10°C 范围)。总电压误差最大值为0.015%,如表4 所总结。
表4. 10ºC 范围内的电压测量误差
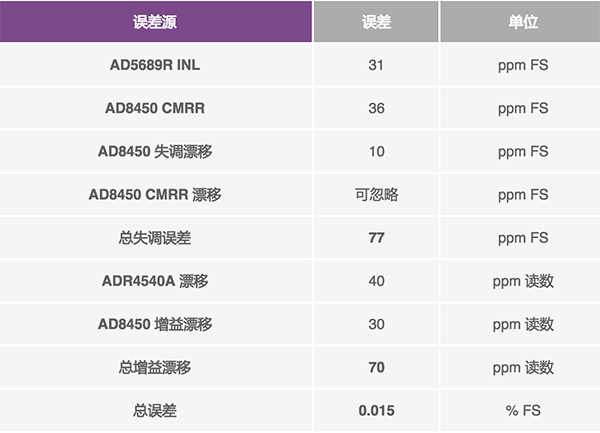
实现高精度电流测量要比高精度电压测量困难得多,因为信号电平更小而动态范围更宽。分流电阻和仪表放大器失调漂移随温度 产生的误差最大。
减少校准时间
系统校准时间可达每通道数分钟,因此减少校准时间便可降低制造成本。若每通道需3 分钟,则96 通道系统便需要4.8 小时来执行校准。电压和电流测量路径有所不同,因为电流极性会发生改变,且失调和增益误差在各种模式下均有所不同,因此需单独校 准。若没有低漂移元件,就必须针对每一个模式进行温度校准,导致校准时间非常长。
当 AD845x在充电和放电模式之间切换时,内部多路复用器将在到达仪表放大器和其他信号调理电路之前改变电流极性。因此, 仪表放大器将始终获得相同的信号,无论处于充电还是放电模式,且增益误差在两种模式下均相同,如图7 所示。多路复用器的电阻在充电和放电两种模式下不同,但仪表放大器的高输入阻抗使得此误差可忽略不计。
从系统设计角度而言,两种模式下具有相同的失调和增益误差意味着单次校准可消除充电和放电模式下的初始误差,使校准时间减半。此外,AD845x 具有极低漂移,对其进行单次室温校准即可, 无需在不同温度下进行校准。考虑到整个系统寿命期间所需的校准,节省的时间可转化为成本的大幅下降。
减少纹波
从线性拓扑转换到开关拓扑后,系统设计人员面临的问题之一是电压和电流信号中的纹波。每一个开关电源系统都会产生一些纹波,但在高效率、低成本要求的PC 和其他大用量电源管理应用中稳压器模块的推动,技术变革非常快。精心设计电路和PCB 布局, 可以减少纹波,使得开关电源可以为一个16 位ADC 供电而不会降低其性能,详见AN-1141 应用笔记用开关稳压器为双电源精密 ADC 供电。此外,ADP1878同步降压控制器数据手册提供有关高功率应用的更多信息。大部分开关电源使用单级LC 滤波器,但 若需要更佳的纹波和更高的系统精度,则双级LC 滤波器将有所帮助。
均流控制
AD8450支持方便的纯模拟均流,是结合多通道实现高容量电池化成和测试的快速、高性价比之选。例如,可以利用一个5 V、20 A单通道设计,三个相同的通道均流后可产生5 V、60 A 系统。采用AD8450 和一些无源器件即可实现均流总线和控制电路。与单通道设计相比,这是一种高性价比方式,因为可以使用低成本功率电子器件,无额外开发时间。详情可参见AD8450 数据手册。
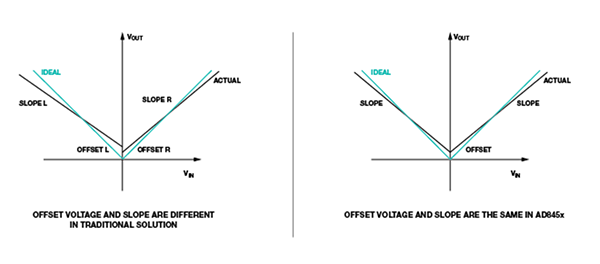
结论
AD8450, AD8451, and ADP1972简化系统设计,具有优于0.05%的 系统精度和超过90%的能效,有助于解决可充电电池制造瓶颈问题,同时为环保技术的普及做出贡献。开关电源可为现代可充电电池的制造提供高性能、高性价比解决方案。
参考电路
Wang, Jianqiang, et al. “Study of High-Capacity Single-Body Li-Ion Battery Charging and Discharging System.” PEDS2009.
Wolter, M, et al. “End-of-Line Testing and Formation Process in Li-Ion Battery Assembly Lines.” 9th International Multi-Conference on Systems, Signals and Devices, 2012 IEEE
作者
Wenshuai Liao
Wenshuai Liao 是ADI 公司位于马萨诸塞州威明顿的线性产品部门(LPG)的一名营销工程师。他在获得清华大学光学工程硕士学位后,曾在大唐电信集团任3G节点BRF工程师三年。他于2002年8月加入ADI公司。
Luis-Orozco
Luis Orozco是ADI公司工业和仪器仪表部的系统应用工程师。主要涉足精密仪器仪表、化学分析和环境监测应用。他于2011年2月加入ADI公司。