随着环境的不断恶化,当前社会越来越重视新能源汽车技术的发展,作为新能源汽车关键零部件(电动机及变速器)的技术发展也越来越受到重视。电动机作为其主要驱动源,变速器则作为动力传输与分配机构,两者的性能设计与相互配合集成研究很大程度上决定了整车的性能。如果电动机温度过高未得到及时散热,则电动机性能就无法得到体现且安全性也会大打折扣,而变速器内部含有被动冷却系统(如AT中的ATF、电驱系统单档减速器中的Mobil等),根据本身结构设计来完成热管理方案。
如在总成结构中能够利用变速器被动冷却系统给予电动机转子或轴心散热,这将是对电动机是两种不同的热管理方案。本文将针对这两种热管理方案利用等效热阻网络法对总成结构(主要针对电动机)的温度场变化进行分析及未来发展趋势分析。
冷却系统研究分析
通常主驱动电动机与变速器在新能源整车中作为两个单独的部件安装,冷却方式也是分开单独考虑。电动机冷却方式主要是靠水冷套外壳冷却,而变速器则靠箱体内的被动冷却系统来冷却,而如果电动机与变速器集成总成结构,需要统筹考虑两者的冷却方式,这样就解决了很多以往存在的不足,例如整车安装得分别考虑电动机与变速器的安装点位置、两者链接处考虑密封等级要求等。电动机与变速器集成总成结构还能更好的发挥出电动机性能和更加完善的利用变速器内部被动冷却系统的利用率,但是其中也有劣势存在。本文将主要针对电动机与变速器的集成总成结构进行热管理分析,鉴于变速器自身被动冷却系统散热效果及结构复杂程度,将主要对电动机部件进行热管理温度分析研究。
总成集成结构中,主要的热传递途径是由热传导和热对流两部分组成,由于热传导途径的传导效率与部件本身的材料属性及接触性能相关性较大,且总成结构在材料属性及结构热属性参数上来说是相对的,故对于分析研究总成结构的温度场分布情况来说,其主要是对其结构的热对流分析(由于总成结构的许用温度始终保持在200°C以下,所以忽略了热辐射的产生)。
1.发热源及边界条件分析
随着新能源汽车技术的发展与改革,对总成结构的集成度及功率密度也要求越来越高。总成部件在运行时其电动机零部件同时会产生转子损耗、定子损耗和绕组损耗等,而变速器部件也会产生摩擦损耗等,这些损耗最终都将转换成热能,促使总成内部各个零部件发热,其边界条件的限制主要是热源的传递影响分析。总成结构中变速器的发热源主要是由齿轮之间摩擦及油与壳体间的摩擦等产生;它们自身的冷却主要是靠被动冷却系统来执行,都能得到较好的散热管理。而电动机中的发热源则集中在定子、转子和绕组等(包括铜耗、铁耗、机械损耗及杂散损耗),针对散热方案可多方面考虑,本文主要对总成结构中的电动机部件进行温度场热分析,通用的冷却方案是主要对定子外围设计冷却水套,使之与整车热管理系统相连,在满足整车热管理的情况下,主动对电动机进行散热冷却。而在集成结构中如能充分考虑箱体内油的冷却作用,将其引入电动机转子轴心处冷却,将是不同模式的热管理方案。
2.电动机结构分析
电动机壳体-水冷套
变速器齿轮组合
电动机驱动轴
变速器壳体
在进行热分析前,首先需观察分析其结构组成形式,结构如图1所示,其由电动机本体结构包括定转子、水冷套前后端盖、变速器壳体结构及内部齿轮组合等构成。
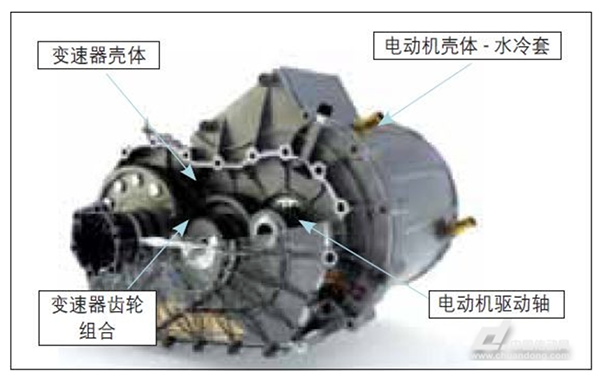
其总成内部结构如图2所示的电动机定子、转子及变速器齿轮等结构构成。
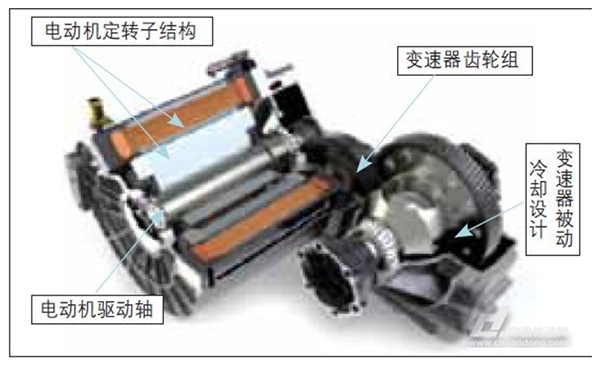
3.电动机冷却方案分析
由于本文所述的电动机结构是与变速器集成一体化集成设计,所以冷却方式除了传统的定子增加水冷套冷却外,还可以考虑利用变速器内部本身的被动冷却系统流动的油液体对电动机转子轴心进行冷却,但是该种方案就面临很多问题,例如变速器内部运转的润滑油的流量与压力是否足够,是否能使之在电动机转子内部运转流动起来、电动机转子进行油冷却是否效果明显等。而接下来将对该两种方案进行具体温度场分析和可行性分析。
电动机热管理分析
根据上文所提到的,本总成结构热分析主要针对于电动机的两种不同的热管理方案分析,通过对比分析电动机内部各零部件温度场分布,从而得出两种方案的差异性和未来发展趋势的可行性。下图3为电动机径向剖面示意图(包括热传递途径)。
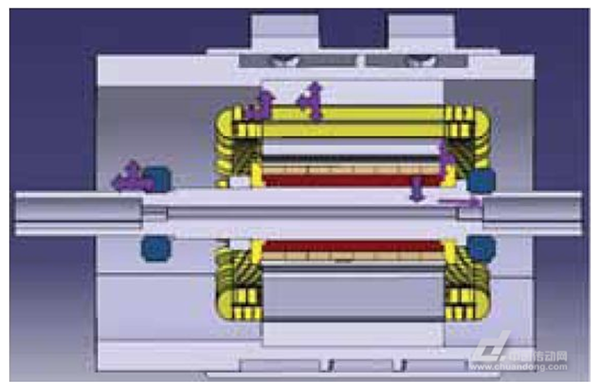
在开始分析两种热管理方案的温度场分布时,假设电动机的热损耗均以热传导及热对流的方式被电动机水套及转子内部油冷给吸收,并转化成为电动机的温升。电动机壳体及端盖、变速器壳体等均处于室温状态,无风条件下,开展此前提下的散热仿真分析。其各个零部件的材料属性及加载的边界条件等设置均为相同的情况下进行分析,且为了简便其前处理、运算过程,对其总成结构的温升模型及导热/散热问题进行如下归纳假设:
(1)总成结构中损耗均转化为热量,且通过散热介质传递;
(2)总成机壳表面的风散热问题暂不考虑;
(3)不考虑材料随温度的变化影响;
(4)不考虑热辐射的影响;
(5)不考虑集肤效应的影响。
1.热管理方案一(仅电动机定子水冷套的热管理方案)
本节主要是在总成结构中电动机冷却热管理只采用电动机定子水冷的情况下,针对电动机各零部件的温度场分析。电动机转子的热传递则主要是先通过转子本身材质的热传导方式到转子表面,然后通过定转子之间气隙空气的热对流传热传输到定子部件上,然后通过定子本身的热传导和水冷套的热对流方式,最终把热量传递散热出去。根据等效热阻网络模型的温度场分布,需要计算出电动机定转子及气隙的材料热性能参数、热对流换热系数等。图4为电动机水冷套的结构示意图。
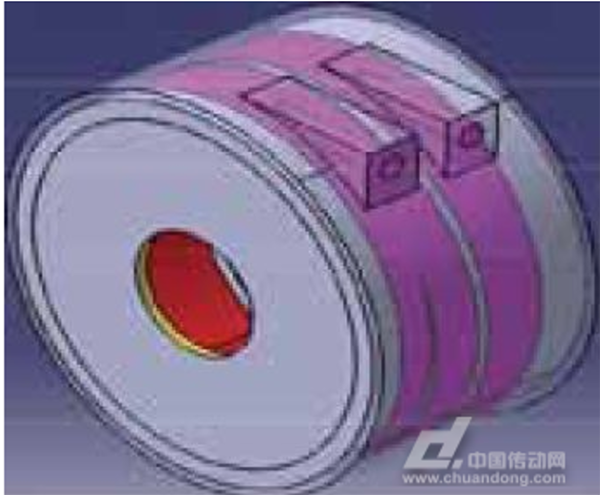
针对电动机本体热管理分析利用等效热阻网络法模型计算;首先需要查出电动机各个零部件的材料热性能参数,其次需要计算出电动机零部件之间存在热对流时的等效换热系数等,例如定子水冷套与水的等效换热系数和定转子之间气隙的等效散热系数的计算等。通过流体力学仿真软件进行仿真计算得出各热传导热对流等需要的参数,最终把各参数带入到等效热阻网络法的数学矩阵模型中,将很简便的得出各零部件的温度场变化情况。
通过电动机水冷套的热管理输入条件和水冷仿真的初始条件,对电动机结构的热传递途径分析,可得出等效模型中所需的热性能参数,并利用仿真软件可得出电动机中水冷模型和定转子之间气隙的等效换热系数h。
而电动机定转子之间的气隙等效散热系数计算稍加复杂,本文采用等效静止空气来计算其换热系数。通过等效定转子之间的气隙模型,查询材料物性参数如普兰特数、热导率、运动粘度和平均比热容等参数,根据流体理论计算公式可得出该气隙的雷诺数、努塞尔特数等参数,最终可得出等效气体的换热系数。
通过上述计算得等效换热系数,再根据结构中存在的热传导与热对流模型,可分别计算出各个零部件的热阻、热容等参数,有了热源、热阻等参数,根据电动机中热分析传递途径可建立等效出热阻网络模型(见图5),由模型可等效出基本数学矩阵模型最后可得出各部件的温度场变化情况,即可作为完整的边界条件计算出有效解,最后可得出总成结构中,电动机热管理方案仅用定子水冷套的情况下,针对电动机在额定工况与峰值工况下电动机各个零部件在稳态运行时温度场变化。
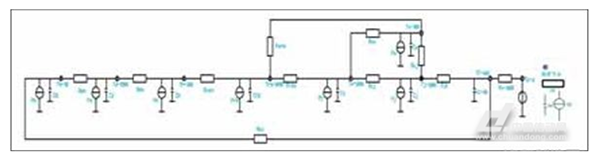
2.热管理方案二(电动机定子冷却加转子油冷方案)
作为整车驱动单元和动力传输单元的集成结构,其有效地控制总成结构的温度变化和温差将是提高整车性能指标的有效手段之一,所以需尽可能地利用总成结构中能够利用的冷却资源。而在总成结构中,变速器或差速器本身的运转将自供冷却模式即被动冷却系统,在集成结构中,电动机与之主要匹配界面为转动部件,如能把被动冷却系统中的油冷系统引入到电动机转动部件中即转子驱动轴中,这将会大大降低电动机转子轴的温差,从而达到减轻电动机定子的水冷要求,即可有效的整体降低电动机温升,最终可达到电动机效率提高和功率密度的提高等性能指标。本节将针对在电动机定子水冷的基础上,增加引入变速器或差速器油冷系统进入电动机转子轴心的热管理冷却方案,利用热阻网络法等效模型计算分析出电动机各零部件的温度场变化情况。
由于针对同一总成集成结构的温度场分析,其中热分析仿真计算中所需的热源、热阻、导热系数及换热系数等热属性参数,均可根据上节内容所得。不同在于额外增加了转子轴心处的热传递途径。电动机转子引入了变速器内部提供的油冷系统,且在这部分油冷系统中油冷的流量及流阻将随差速器转速的不同而变化。所以在不同工况下,电动机转子的冷却效果乃至整个电动机的冷却效果将随之变化,鉴于工况的复杂程度,在此仅针对电动机在额定和峰值工况下的冷却效果进行温度场分析。由于电动机转子即电主轴引入了冷却流道,从而在该节点上增加了热对流的传递途径,即转子热源传递路线使之由原来只向定子侧传递途径增加为既向定子侧传递,又能通过转子轴心油道的热对流传递。
在此鉴于引入变速器或差速器的油冷系统的复杂性(涉及到冷却油道、挡油环等一系列结构优化设计),暂不对引入油冷系统的复杂结构进行详细分析。仅假设在整车处于电动机额定工况与峰值工况下时,等效变速器或差速器的被动冷却系统为油泵处理(在油道及挡油环等影响油流动的结构一定的情况下),得出油道引入到电动机转子轴心处的压力P与流量q数值。可得出电动机的等效热阻网络模型(见图6)。由上述所述方法计算出转轴油道中的对流等效换热系数等参数。根据等效数学矩阵模型得出电动机各个零部件在稳态运行状态额定工况与峰值工况下的温度场变化情况。
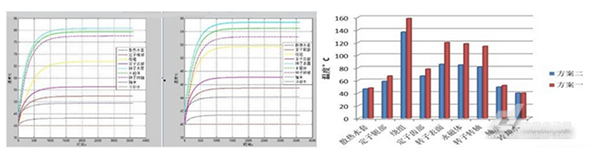
由此可知,由于减小了转子部件之间的热阻,均匀的剖分了转子轴心的热损耗,显而易见的降低了转子的温升,也间接的降低了定子水冷套的散热压力,从图可知不同工况电动机零部件降低的温升也不同,但整体温升均有降低,即降低电动机定子水冷套的冷却要求或使电动机整体散热更加均匀有效,对整车热管理要求也随之降低。
电动机热管理可行性方案分析
通过上文介绍,对总成结构中电动机两种不同热管理方案的温度场变化对比(见图7、图8)可知,电动机转子轴心处引入被动冷却系统的油冷系统的散热效果将有效的降低了电动机内部的温差,特别对于电动机转动部件。但如能在满足电动机本身的散热要求情况下,只用定子水冷套热管理方案,将大大减少了一系列问题,例如可减少电动机制造成本,加工工艺,及可不用考虑电动机转子的密封及强度等问题。而如在强调电动机性能效率和功率密度的前提下,对电动机转子轴心引入该热管理方案将十分有效,虽其中也将面临一系列问题,但在强调集成度及功率密度比的前提下,这将是未来发展的一个趋势。
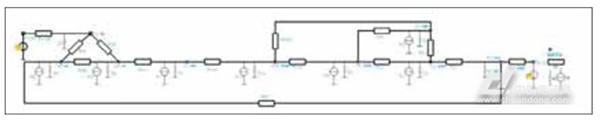
结语
针对电动机定子水冷套的前提下增加转子轴心油冷(来自变速器或差速器被动冷却系统),具体可行性方案及存在的问题分析是:
1.电动机转子冷却来自差速器
(1)取决于变速器的排列方式,在变速器内需设计特殊的挡油环及冷却油道,差速器转速决定了被动冷却系统油飞溅能力,是否能够使油飞溅到电动机转子轴心油道里,然后再返回变速器油道中;
(2)由于变速器用电磁阀或分离泵使冷却循环起来的油的流量将不受控制。油流量将受到差速器转速的影响,冷却流量或者冷却能力是否满足,通常需要一系列测试确定其冷却能力,后续再优化油道或挡油环(通过CFD仿真计算出合理的流量流速)。
(3)冷却油循环系统中油压非常低,接近大气压,约0.2~0.3MPa,如何得到进出口的油压差。
2.冷却油来自变速器(来自变速器冷却循环),需考虑单独增加的冷却泵或电磁阀控制。
(1)冷却油压是否足够(大约0.3~0.5MPa,最高不超过0.8MPa);
(2)冷却流量:取决于电动机转子冷却要求-进出口温差和系统中冷却液的冷却能力等。
另外,油的热容量较大,且具有较好的介电能力,是一种比较理想的直接的冷却介质,但油本身存在粘性,搅动过程中多流层会产生内摩擦发热。电动机冷却油道设计不合理,会出现油和发热器件接触不充分不能有效带走器件热量,或加剧冷却油的内摩擦,电动机的冷却效果较差,甚至会出现温度不降反升,因此,油冷电动机中冷却油道的设计合理性对冷却至关重要。
综上所述,从稳态角度开展电动机不同冷却热管理方案的温度场分析可知;如从总成结构的制造成本及运行安全风险等评估,在满足热管理方案要求下,仅用电动机定子水冷套形式是最为妥当。但在强调总成电动机的功率密度、有效输出率和结构体积等性能参数时,则需要尽可能降低其温升,即尽量减少零部件的节点温度。通常电动机运行时转动部件的温升相对比较高难以散热,转子引入油道冷却就显得尤为必要。且从上述分析可知,其结构设计也具有可行性。这也是在未来越来越强调集成度及功率密度等参数的前提下,势不可挡的一个研究趋势。
本文来源:电动机与变速器总成的热管理分析