作者:Mike Delaus和Santosh Kudtarkar(ADI公司)
在医疗设备设计领域,一个重要趋势是提高这些设备的便携性,使其走近病人,进入诊所或病
人家中。这涉及到设计的方方面面,尤其是尺寸和功耗。晶圆级芯片级封装(WLCSP)的运用对减小这些设备电子组件的尺寸起到了极大的助推作用。
此类新型应用包括介入性检测、医学植入体和一次性便携式监护仪。但是为了最大限度地发挥出WLCSP封装在性能和可靠性方面的潜力,设计师必须在印刷电路板(PCB)焊盘图形、焊盘表面和电路板厚度的设计方面贯彻最佳实践做法。
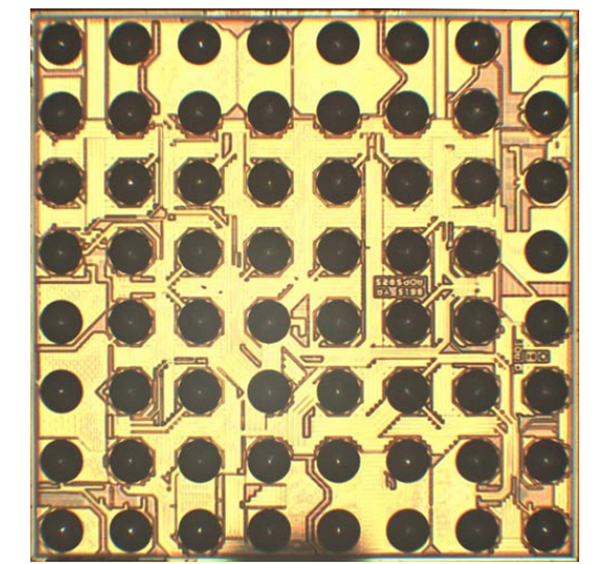
晶圆级芯片级封装是倒装芯片互联技术的一个变体(图1)。在WLCSP中,芯片活性面采用反转式设计,通过焊球连接至PCB。一般地,这些焊球的尺寸足够大(0.5 mm间距,回流前为300 µm,0.4 mm间距,回流前为250 um),无需倒装互联技术所需要的底部填充。该互联技术有多个优势。
首先,由于消除了第一级封装(塑封材料、引脚架构或有机基板),因而可以节省大幅空间。例如,一个8引脚WLCSP所占电路板面积仅相当于一个8引脚SOIC的8%。其次,由于消除了标准塑封中使用的线焊和引脚,因而可以减小电感,提高电气性能。
另外,由于消除了引脚架构和塑封材料,因而可以减轻重量,降低封装厚度。无需底部填充,因为可以使用标准表贴(SMT)组装设备。最后,低质芯片在焊锡固化期间具有自动对齐特性,有利于提高装配成品率。
封装结构
WLCSP在结构上可分为两类:直接凸点和再分配层(RDL)。直接凸点WLCSP包括一个可选的有机层(聚酰亚胺),充当芯片活性面的应力缓冲层。聚酰亚胺覆盖着芯片上除焊盘周围开口之外的所有区域。该开口上喷涂有或镀有一层凸点下金属(UBM)。UBM由不同的金属层叠加而成,充当扩散层、阻挡层、浸润层和抗氧化层。将焊球滴落(这是其称为落球的原因)在UBM上,并经回流形成焊接凸点(图2)。
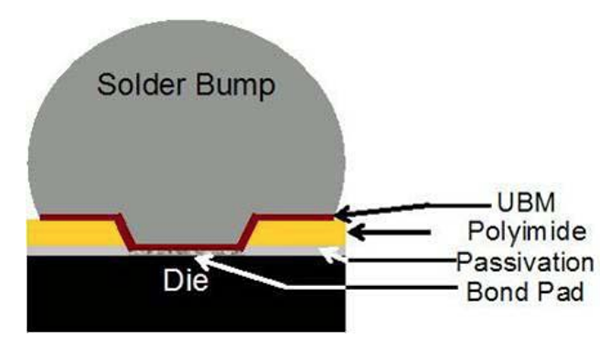
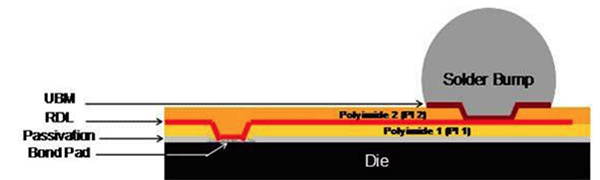
运用RDL技术,可以把针对线焊设计的芯片(焊盘沿外围排列)转换成WLCSP。与直接凸点不同,这类WLCSP采用了两个聚酰亚胺层。第一个聚酰亚胺层沉淀在芯片上,使焊盘保持开放。然后喷涂或镀上一层RDL,把外围阵列转换成面积阵列。然后,构造工艺与直接凸点相同,包括第二层聚酰亚胺、UBM和落球(图3)。落球后则是晶圆背面研磨、激光打标、测试、分离及卷带和卷盘。在背面研磨工序之后,还可选择施用背面层压板,以减少切割时造成的芯片脱离问题,简化封装处理工作。
最佳PCB设计实践电路板设计的关键参数为焊盘开口、焊盘类型、焊盘表面和电路板厚度。基于IPC标准,焊盘开口等于UBM开口。对于0.5 mm间距WLCSP,典型焊盘开口为250 µm,0.4 mm间距WLCSP为200 µm(图4)。

阻焊层开口为100 µm与焊盘开口之和。走线宽度应小于焊盘开口的三分之二。增加走线宽度可以减少焊接凸点的支柱高度。因此,维持正确的走线宽度比对于确保焊点可靠性也很重要。对于电路板制造来说,表贴装配使用两类焊盘图形(图5):
• 非阻焊层限定(NSMD):PCB上的金属焊盘(I/O装在其上)小于阻焊层开口。
• 阻焊层限定(SMD): 阻焊层开口小于金属焊盘
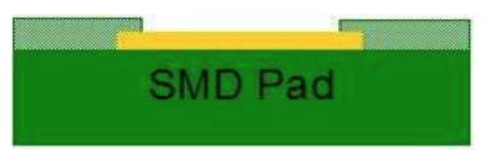
由于铜蚀刻工艺比阻焊开口工艺有着更加严格的控制,因此NSMD比SMD更常用。NSMD焊盘上的阻焊开口比铜焊盘大,使焊锡可以依附于铜焊盘四周,从而提高焊点的可靠性。
金属焊盘上的表层对装配成品率和可靠性都有着深刻的影响。采用的典型金属焊盘表面处理工艺为有机表面防腐(OSP)和无电镀镍浸金(ENIG)两种。金属焊盘上OSP表层的厚度为0.2 µm至0.5 µm。该表层会在回流焊工序中蒸发,焊料与金属焊盘之间会发生界面反应。
ENIG表层由5 µm的无电镀镍和0.02 µm至0.05 µm的金构成。在回流焊过程中,金层快速溶解,然后,镍和焊料之间会发生反应。非常重要的是,要使金层的厚度保持在0.05 µm以下,以防形成脆性金属间化合物。标准的电路板厚度范围在0.4 mm至2.3 mm之间。选择的厚度取决于已填充系统组件的鲁棒性。较薄的电路板会导致焊接接头在热负载条件下的剪切应力范围、爬电剪切应变范围和爬电应变能量密度范围变小。因此,较薄的积层电路板会延长焊接接头的热疲劳寿命。
测试和评估
结合前述变量,WLCSP的可靠性通过对器件进行加速压力测试来评估,此类测试包括高温存储(HTS)、高加速压力测试(HAST)、高压锅测试、温度循环、高温工作寿命测试(HTOL)和无偏高加速压力测试(UHAST)。除了热机械诱导性压力测试以外,还要进行坠落、弯曲等机械测试。
HTS测试旨在确定在不施加任何电应力的情况下,高温条件下长期存储对器件的影响。该测试评估器件在高温条件下的长期可靠性。典型测试条件为在150°C和/或175°C下持续1000小时。实施测试时要把器件暴露在指定环境温度之下,并持续指定的时长。