作者:Aengus Murray
国际能源报告显示,2006年电子电机的能耗为全球电能消耗总量的46%,相当于6040 Mt CO2排放量1。这导致人们要求电机驱动器制造商新增高级控制功能和工具,以便优化系统能效。在工厂生产系统中优化能效的新电机驱动器生态系统已得到了全球范围内的广泛认可。对于欧洲来说,得益于节能政策,工业电能消耗量呈现出每年1%的下降趋势2。
工厂中最常用到电机的地方是电泵、风扇、压缩机和运输机,且电机在这些应用中大多属于标准产品。小型机器设备中使用的小型电机(低于0.75 kW)占全球存量的90%,但电机能耗不到总量的10%。然而,中等尺寸(0.75 kW至350 kW)的工业电机几乎占全球电机能耗的70%。在一个典型应用中,仅有50%的系统能耗转换为有用的机械能,这引起了全球能源法规制定者和厂商的重视。过去几年来,美国、中国、欧洲和其他地区的监管机构引入了最低能耗性能标准(MEPS)。优质电机的额定能效等级现在可从最低功耗范围时的80%到最高时的96%,因此厂商开始在电机以外寻求节能手段。

图1描述了现代工厂中自动化机器或过程的主要元素。这种方式提供了优化机器运行和过程的全新思路,将能效和生产率提升到新的高度。
电机的效率和总体生产过程由多个控制层决定。第一个控制层调节功率逆变器的开关顺序,控制电机电压和电流以及最大扭矩生产率。第二层是位置和速度控制器,高效率运作机器。在过程设备中,它可以驱动最优泵流速;而在自动化设备中,它可以是执行装配功能的速度或位置命令序列。如果是后一种情况,则速度控制的响应时间相比扭矩生产率而言对机器控制器更为重要。通信和系统层的重要性日益凸显,因为多个电机现在通过高速数据网络同步,并连接工厂网络。过程管理器可在需要的时候顺序开启机器,而不是让它们在空闲模式下等待。联网安全功能实现设备的高效启动和停止,最大程度缩短停机时间。工厂管理人员跟踪电机驱动器的操作,并诊断数据,以便改善过程能效和可靠性。
高效扭矩产生: 算法和以太网
电机效率是任意给定速度和终端电压下每安培所产生扭矩的函数。电子电机通过试图将其内部磁场拉至对齐位置的力产生扭矩。在图2交流电机中,这些力通过定子和转子磁场的相互作用产生。当定子电流与转子运动同步时,交流电机产生恒定的扭矩,维持连续场的不对齐状态。交流电机速度与电机电流频率直接相关,且需要使用可变频率电压源才能进行速度控制。当转子和定子的磁场对齐误差达到最大时,效率最高。电机效率还取决于电机结构,尤其是转子磁场结构。在异步感应电机中(AIM),电流流过转子和定子绕组,部分最小定子电流消耗在使磁芯磁化上。永磁同步电机(PMSM)效率更高,因为它们无需任何电流来使转子磁场磁化。借助于突出的磁芯结构,超高效率内部永磁(IPM)电机能够产生额外的扭矩。

以上所有电机都用于工业中,具体取决于功率和应用要求,但由于结构简单、使用方便,异步感应电机是目前为止最常用的电机。永磁同步电机具有较高的扭矩重量比,其低惯性转子结构使其非常适合自动设备的高动态控制应用。然而,AIM可在直接连接三相交流线的时候启动,并且可以使用简单频率逆变器控制速度。以前不像现在那么重视效率,一般是直接把风扇、泵或压缩机连接到交流线上,并通过阻尼器、阀门或简单的开/关控制这个过程。以50%速度运行时,开环频率控制可将离心泵的功耗降低至不足全功率的20%;而使用开/关控制使流速下降到50%时,功耗为全功率的50%。这种系统效率提升促使厂商改造现有固定速度电机应用的变频器。近来,高级算法可以通过微调定子电压来调节转子磁场,进而优化效率。驱动器制造商现已开始提供标准驱动箱,可配置为各种电机型号与类型。
最新的模拟和数字信号处理设备甚至在成本敏感型变频器应用中引入了高级控制功能。估算算法仅测量定子电流和电压便可计算出转子磁场的角位置。这些无传感器控制算法简化了高效率IPM电机的部署,并最大程度提升压缩机和运输机等应用的处理效率。诸如绕组机器或大型泵等较高功耗应用依然倾向于采用感应电机,但500 kW电机的典型效率可高达96%。这些驱动器内置的算法通常可以优化电机效率,并监控驱动器的工作情况。一般而言,这些驱动器采用串行现场总线连接,允许本地PLC记录运行和诊断数据。一个不断增长的趋势是使用诸如Ethernet/IP或Modbus TCP等工业以太网协议将驱动器连接到工厂网络中,以便通过协调多个驱动器运行而改善效率。
高效运动控制: 精确隔离和通信
精确运动控制加上精确通信时序,可缩短机器生产周期,降低生产每个部件所消耗的能源。由于设备的资本投入,这一点在机器生产率和质量通常比电机能效更重要的自动化系统中很重要。驱动器制造商通过PMSM伺服电机和驱动器支持自动化应用;这些电机和驱动器设计为可在速度和位置控制中实现快速响应和高精度。快速控制处理器配合精确电压驱动器和电流反馈,可提供平滑的动态扭矩控制。功率变频器中的高电压和电流对电路设计人员来说是一种挑战,因为隔离电路必须满足严格的电气安全标准。高速磁隔离技术支持模拟和数字信号电压的安全隔离,且不会降低速度或精度性能。编码器处内置的精密模数转换器可提供高达24位分辨率的位置反馈,从而在低至1 RPM的速度下实现高动态速度控制。这种性能水平可支持的自动化应用有:精密机器部件的多轴铣磨、精细几何集成电路的装配,或手机部件的注塑成型。除了控制精度,电机运动时序还需紧密同步,因为时序误差
直接导致多轴位置控制的轨迹误差。诸如PROFINET和EtherCat等同步工业以太网协议采用经过修改的以太网网络接口,支持数据的实时同步,且时钟抖动低至1 μs。这些网络接口支持全部两种同步运动控制,可实现生产系统管理的高生产率和工厂网络连接性。工程效率:快速定制建模工具可让驱动器公司为最终应用快速定制控制算法,无需在工厂中投入大量试生产和误差调谐。
自动化机器是复杂的互连系统,需要跨学科工程团队的支持。图3仅显示支持开发自动化设备开发所需的部分关键设计功能。一般而言,很多这类工程师供职于不同的公司,因此供应链上的不同供应商必须为设计人员的整合工作提供支持。MathWorks等公司提供的建模工具支持完整的系统模型,包括状态控制、运动算法、电机和机器负载。特殊的电磁和机械设计工具可以生成交流电机和机器的行为模型,增加系统模型的精度。虽然无法完全自动化整个设计过程,但可以大幅减少原型制作次数。新电机或机器的控制算法可在进行原型制作前于仿真平台上完成开发和测试。自动代码生成工具允许在测试平台上快速部署控制算法。每一次设计迭代都提供新的数据,改进系统模型的精度。自动生成的控制代码加上经过验证的系统应用代码,可以用于生产驱动器系统中。因此,驱动器公司可快速部署针对特定应用优化的新控制功能,进而优化能效和自动化生产率。
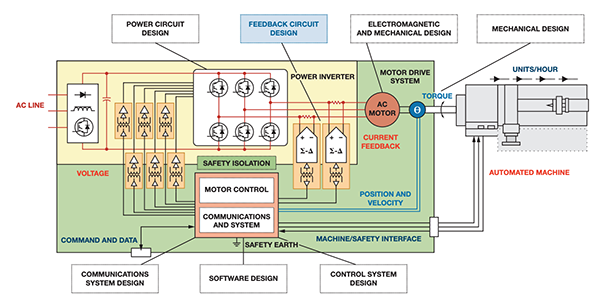
结论
越来越多的工业和仪表应用要求使用精密转换器来实现各种工艺的精确控制与测量。此外,这些最终应用还要求更高的灵活性、可靠性和功能集,同时降低成本和电路板面积。元件制造商正在解决这些难题,并推出了一系列产品来满足系统设计人员对当前与未来设计的要求。如本文所述,有多种途径可选择合适的元件用于精密应用,每一种都各有优缺点。随着系统精度的提高,人们需要更加注重合适元件的选择,以满足应用要求。有关文中涉及产品的更多信息,请访问:www.analog.com/cn/motorcontrol
参考文献
1、 Conrad U. Brunner 和 Paul Waide. “Energy-Efficiency Policy Opportunities for Electric Motor-Driven Systems (节能政策赋予电机驱动系统的良机) ”。国际能源署工作文件,2011。
2、欧洲电气工程师协会工作小组。“Electrical Power Vision 2040 (2040年电力愿景) ”。 欧洲电气工程师协会秘书处,2013年2月。注意:CO2排放单位为Mt,其中:1 t = 1000 kg。